The Role of Industrial Process Pumps in Modern Manufacturing
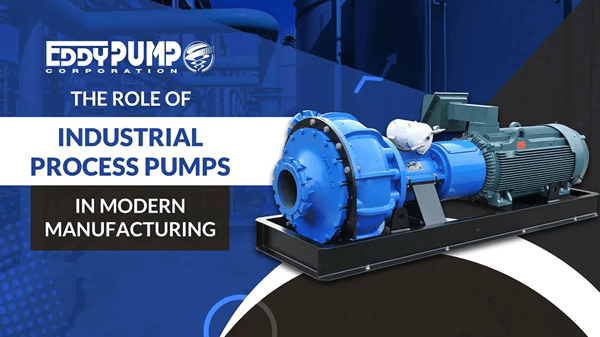
In the competitive world of modern manufacturing, efficiency and reliability are paramount. Industrial process pumps, essential components in many manufacturing processes, drive the movement of fluids such as water, chemicals, slurries, and oils through various production stages. Their seamless operation ensures that factories and plants maintain productivity, quality, and safety standards by enabling fluid transfer, ensuring proper flow rates, and maintaining necessary pressure levels.
Understanding Industrial Process Pumps
Industrial process pumps are specialized devices designed to move fluids—liquids, gases, and slurries—through various stages of a manufacturing process. They convert mechanical energy from a motor into hydraulic energy, creating a pressure differential that drives fluid flow from areas of high pressure to low pressure, ensuring continuous and controlled movement.
Types of Industrial Process Pumps
- Centrifugal Pumps
Centrifugal pumps use a rotating impeller to generate flow, ideal for transferring low-viscosity fluids at high flow rates. Typical applications include water treatment, chemical processing, and HVAC systems.
- Positive Displacement Pumps
Positive displacement pumps move fluid by trapping a fixed amount and forcing it through the discharge pipe. They are suitable for high-viscosity fluids and precise flow control applications in the oil and gas, food and beverage, and pharmaceutical industries. Types include gear pumps, vane pumps, and peristaltic pumps.
- Diaphragm Pumps
Diaphragm pumps use a flexible diaphragm to move liquids, perfect for handling abrasive or corrosive substances. They are widely used in chemical processing, wastewater treatment, and mining operations.
- Piston Pumps
Piston pumps use a reciprocating piston to move fluid containing suspended solids. They are highly effective for pumping high-viscosity fluids. Due to their precise flow control and reliability, piston pumps are ideal for hydraulic systems, oil and gas production, and industrial cleaning applications.
Maintenance and Troubleshooting
- Best Practices for Maintenance
Maintaining industrial process pumps involves several best practices to ensure longevity and optimal performance. Regular lubrication of moving parts, checking for proper alignment, and ensuring that seals and gaskets are intact are essential. Cleaning the pump and its components to remove debris or corrosion is crucial. Following the manufacturer’s maintenance schedule and using recommended parts and lubricants will help keep process pumps in top condition.
- Common Issues and Solutions
Common issues with industrial process pumps include cavitation, leaks, and overheating. Cavitation occurs when vapor bubbles form in the pump, causing noise and damage. This can be addressed by ensuring proper pump selection and adequate suction pressure. Leaks often result from worn seals or gaskets and should be fixed by replacing these components. Overheating can stem from excessive friction or inadequate cooling, mitigated by proper lubrication and functioning cooling systems.
- Importance of Regular Inspections
Regular and proactive maintenance is crucial for the reliability and efficiency of process pumps. Routine checks can identify potential issues before they become significant problems, reducing the risk of unexpected downtime and costly repairs. Proactive maintenance, such as replacing worn parts and monitoring pump performance, extends the lifespan of industrial process pumps and ensures consistent operation.
Innovative Design Features Enhancing Efficiency and Reliability in Modern Industrial Pumps
Modern industrial process pumps have cutting-edge design features that significantly enhance their efficiency and reliability. Key innovations include:
- Variable Frequency Drives (VFDs): Variable Frequency Drives control the pump speed and energy consumption, optimizing performance and reducing energy costs.
- Magnetic Drive Systems: By eliminating seals, these systems minimize the risk of leaks, improving safety and reducing maintenance requirements.
- Self-Priming Designs: These allow pumps to start automatically without manual intervention, enhancing operational efficiency and convenience.
These advancements in chemical process pumps and other industrial pumps lead to superior performance, lower operational costs, and increased safety across various industrial applications.
Conclusion
Industrial process pumps are vital for maintaining manufacturing efficiency, reliability, and safety. From ensuring hygiene in the food and beverage industries to handling corrosive materials in pharmaceuticals and supporting critical operations in automotive and textiles, these pumps are indispensable. Industries can maximize efficiency, reduce operational costs, and ensure safety by choosing the proper industrial pumps for specific applications.
For expert advice and tailored solutions, contact EDDY Pump. Their team of specialists is dedicated to helping you find the best process pumps and equipment for your unique needs, ensuring you benefit from the latest advancements in pump technology.